- Location
- Toronto, Ontario, Canada
- Resume
- 0ZION JING resume2.docx
- Portals
-
-
Toronto, Ontario, Canada
-
- Categories
- Data analysis Mechanical engineering Robotics Hardware product design Project management
Skills
Socials
Achievements
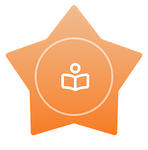
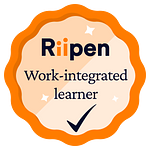
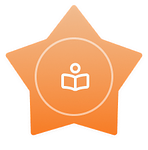
Latest feedback
Recent projects
Work experience
Process Engineer (Electric Cabinet-Sheet metal parts)
SK Electric Canada Inc
July 2024 - September 2024
Worked on Electric Cabinets body manufacture, products supplied to HUSKY,GE
Collaborated with global engineering team on new equipment and machinery, optimize product manufacture process and ERP process in new plant; Implemented Trouble-shoot process and corrective actions. - Applied OneNote to prepare ERP instruction manual for later reference.
Sourcing of components, equipment & tools for manufacture plant acc. to the project milestone.
-Negotiated with suppliers, helped to save 30% of forklift rental costs through multi-supplier bidding.
Reviewed with supplier on SK technical SPEC to make sure their equipment meets SK requirements.
-For Nederman Dust-Collector Equipment Project, re-measured the plant, updated the layout, and provided detailed modification suggestions; close communicated supplier to ensure timely delivery.
Monitored production metrics and conducted regular audits to ensure compliance with quality standards and continuous improvement actions. Evaluated manufacturing process to identify inefficiencies. -Created Excel program to make tooling selection process more efficient, save 50% working time.
Senior Application Engineer & Project Manager (Valve Train)
Schaeffler Trading Shanghai Ltd
Shanghai, Shanghai, China
August 2016 - October 2022
Managed engine parts projects for global OEMs (BYD, Changan, GM, VW), including roller finger followers, hydraulic lash adjusters, tappets, HP pump lifters.
Interacted closely with customers to understand their requirement and identify new opportunities, promoted products and technology; -Helped Schaeffler getting new businesses every year.
Designed and developed products (2D&3D), verified GD&T and interference compliance, performed CAE calculations (kinematic and FEA), managed CAD approvals and formally released drawings to customer. – Created and applied self-made Excel program to facilitate verification process, save 25% working time.
Utilizing SG project management method, as PM presented project status in gateway meetings with global directors; Led project team to collect project/technology/production data for TR meeting; Arranged & supervised DVP&R plan, followed up tooling and samples preparation from prototyping to mass production; arranged CAE team for simulation (eg. FEA, Dynamic) and the labs for test (eg. Engine & cylinder head test, Mechanical and material test (eg. Hardness, Metallurgy, Tensile); reported any failure and took measures to minimize potential risk; updated DFMEA. -Ensured projects safe launch on time, in budget, 0 customer complaint.
Led cross-functional teams in root cause analysis and corrective action implementation for product issues, utilizing on-site investigations and statistical data analysis to solve problems. –Real case: investigated OEM engine oil pressure issue on production line, through test data analysis and parts measurement to find the Root cause and finally solved the problem, reduce potential economic losses by 500K.
Led innovation workshops (e.g., VAVE) to identify cost reduction opportunities while enhancing product performance and customer satisfaction, fostering a culture of continuous improvement. -Statistical analyzed the technical trend of RFF&HLA parts through investigating parts feature and related market volume data.
Arranged benchmarking study to identify potential innovation and improvement; provided trainings on product application, failure mode & calculation. -Generated formal guidance & calculation tables for trainees.
Application Engineer (Variable Valve Train)
Delphi Shanghai Dynamics & Propulsion Systems Ltd.
Shanghai, Shanghai, China
August 2011 - July 2016
Worked on variable valve timing components (Oil Control Valve with Electric Solenoid & Variable Cam Phaser) for Peugeot Citroen, Dongfeng-Citroen, Changan-PSA, and Chery Group projects
Acted as the main technical liaison with customers, ensuring their requirements were met throughout the product lifecycle.
Communicated design/product issue and reviewed technical issues with customers and tech-centers. Participated in development and implementation of CVM (Components Verification Matrix), DFMEA; Led return parts inspection/analysis. Reviewed and released drawings/BOMs to plant. Provided technical input to ensure proper test and validation plans are developed and implemented.
Led root cause analysis of product and manufacture failures with DOE experiments. –Real Case: for VCP assembly product line, through Shinning method to analysis the key factors of VCP resistance torque high problem.